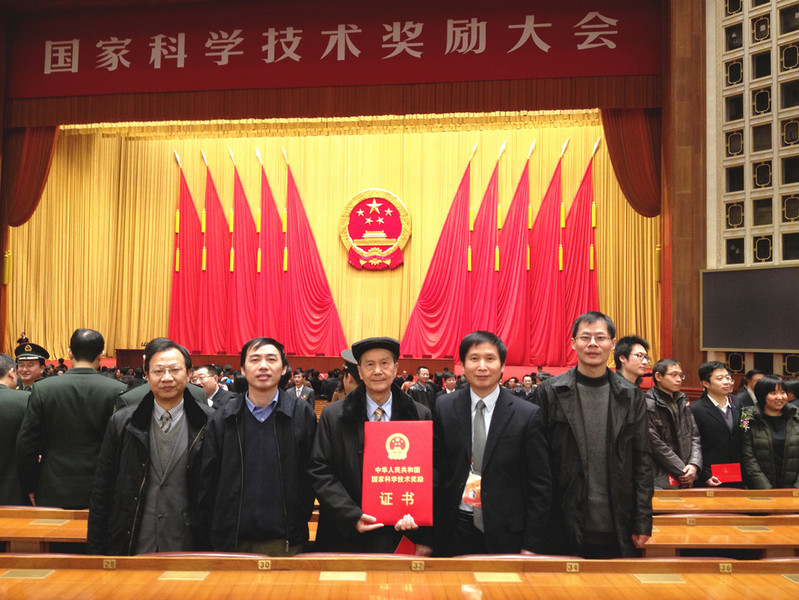
液压团队主要成员。从左到右:曾良才、傅连东、湛从昌、陈奎生、陈新元
记者 程毓
在湖北麻城的大别山电厂,一辆满载煤矿的火车驶入卸载车间。一节节车厢依次被翻车机夹住、翻转,卸煤后驶出车间。整个过程连贯高效!这套设备是由js官网机械学院液压团队研发,深受企业好评。
解决大别山电厂的翻车液压系统问题
三年前,大别山电厂采用的进口翻车机液压系统经常出故障,造成停工停产,严重影响企业的正常经营。他们慕名找到js官网液压团队,提出改造整个液压系统。
湛从昌教授带领液压团队,在充分了解设备现状和使用需求后,建议“把装在翻车机上的液压系统和油箱,改为装在地面上。”既减轻翻车机旋转的重量,又使翻车机平稳运行,还方便检修。“啊,从来没听见过这样装的。”该企业技术人员听后将信将疑。
毕竟是新思路,真正做起来遇到了一系列技术难题。液压系统和油箱拆了后,翻车机的重心改变了,老师们重新做仿真数据分析;翻车机翻转的力改变了,相关技术参数需要调整;连接油箱和液压缸的钢管,为了便于旋转改成了软管,如何防止磨损……
设计图纸、调整参数、给软管安托架……用了半年,一个个难题解决了,又用了半个月完成了安装。试车前的晚上,老师们紧张得睡不着,反复预想可能出现的问题和解决的方案,一直到深夜。
试车时,公司老总和中层干部几十人来到现场观看。打开电闸,一节节车厢被夹住、翻转。“一切顺利!” 第一条装卸线改造成功后,该公司又把另一条的改造交给了该团队。
运行三年来,全国各地的企业来参观学习,看了都竖起大拇指夸赞,“国产化的液压系统很好用。”作为新中国成立以来,麻城境内投资最大的重点项目——大别山电厂,也保障了华中地区用电需求,促进了华中地区经济社会发展。
改造武钢四条生产线的液压电控系统
液压团队做的合同金额最大、时间跨度最长的项目,是用10年改造武钢4条生产线的液压电控系统。
2004年,武钢热轧厂从日本引进的四条生产线液压设备已使用十多年,其中的关键元件“加减速阀”磨损严重。因为国外不提供,它又不是标准件,无法购买更换,生产线随时可能停摆。停一分钟,造成的损失就有数十万、上百万元。于是,他们找到js官网液压团队。
“用我们先进的液压技术进行改造。”该团队提出解决方案。基于校企合作多年的相互信任,武钢决定先停产1台进行改造,与js官网液压团队签下600万的项目合同。“在当时,这是js官网历史上金额最大的企业项目。”液压团队的“元老”湛从昌自豪地介绍。
原来的“加减速阀”是开关型,需要人工调整大小。现在改为先进的电液比例伺服阀控制,不仅需要开发整个液压系统的控制软件,精确控制重达上千吨的步进梁,还要根据信号实现供油量和运行速度的自动调整……形成闭环控制系统。
液压团队的老师们分工合作,有的开发软件、有的设计图纸、有的计算油量和速度。经过一年多的技术攻关,他们攻克了一个个难题,完成了整条生产线的改造。运行的当天,武钢公司领导现场观看。“3、2、1,启动!”“运行正常,成功!”
随后,每2-3年改造一条生产线,到2015年完成了全部4条线的改造,总项目金额2300万元。2012年统计3条线近3年带来的经济效益,为6亿余元。
发明间隙密封液压,替代进口产品
我国是钢铁大国,钢铁产量世界第一。但是,冶金设备的核心部件——重载高频液压元件仍主要依赖进口。2011年,我国相关元件进口率达90%左右。
上世纪八十年代初,js官网有了液压团队。在给企业培训员工时,经常听到学生们讲述生产中的问题,老师们竭尽所能地帮忙解决,而且大多免费“义诊”。老师们说:“为企业服务就是为国家做贡献。”
企业的难题也成了老师们的课题。液压团队的老师们潜心研究,发表了不少论文,也下决定要改善中国国产冶金设备“空壳化”,助推实现“国产化”。
广东韶关液压件厂2007年联系该团队,提出联合开发间隙密封液压缸。之前,该厂多次研制、仿制液压缸,都不尽人意。正值壮年的湛从昌受邀前往该厂,参观了生产线,了解了技术力量后,感觉还不错,就欣然同意合作。
通过学习国外的液压缸技术,分析国内的液压缸试验品,湛教授创新性地提出“取消普通液压缸活塞橡胶密封圈,通过间隙配合实现密封”的技术路线,并通过实验数据,提供出各种参数,指导提高控制间隙的精度。
该厂成功生产出“低摩擦恒间隙密封伺服液压缸”,不仅打破了国外的垄断,而且出口到印度、越南等国。武科大液压团队在行业里进一步扩大了影响力。
之后,为了提高液压缸的稳定性,湛教授团队试着改变活塞的形状,设计“变间隙密封液压缸”,使之根据压力产生弹性变形,自动调整间隙大小,减少油量的泄漏,不仅提高了两个轧辊的稳定性,还降低了液压油的使用量,达到提高质量和节能增效“双效应”。
该技术在当时为国际首创,申请了5项专利。之后,该团队开发多个系列的元件,在全国50多家冶金企业生产线上推广应用。
首创液压缸试验方法,制定国家标准
“我们设计和制作的设备,整整装了11个火车车皮。运到攀钢后,安装用了半年,建成一个足球场大小的、西南地区最大的液压检测中心。”湛从昌回忆20多年前的难忘经历。
上世纪八十年代,武钢从德国、日本引进了热轧、冷轧生产线,大量的液压元件需要抽检。原冶金部领导考察多家单位后,确定武科大液压团队负责筹建测试试验台,并拨给专款建设。该团队用了一年时间,建设了泵、阀、缸、元件检测台。国外专家来校视察后表示满意,认可检测结果。“为武钢把好了‘进口关’。”湛老师说。
1993年,攀钢获此信息,请求帮忙建设“液压检测中心”,湛从昌毫不犹豫地接下来。因为工程量大,他四处招兵买马,在学校里寻找会画图的老师,从武钢请来退休的工程师,又死磨硬缠地租来校内的闲置场地,就开始做起来。
没有计算机,全部图纸靠人工一张张绘制,还要描图、晒图,再找企业按照图纸加工,然后一台台组装。一年半过去了,在液压实验室里,一面墙的柜子堆满了图纸。所有设备终于研制出来后,从武汉运到攀枝花,攀钢使用后评价,“检测方便,效果也好。”
原冶金部得知后,主动欢迎申报科技奖。于是,湛老师邀请专家鉴定,原冶金部组织评审。1995年,该技术获得冶金部科技进步二等奖,是武科大最早获得的部级奖励之一。攀钢“液压检测中心”经过几次升级,至今仍在使用,为企业源源不断地创造着利润,是企业的“摇钱树”。
受益这个项目,液压团队也成长起来,成为拥有液压、电控、计算机、机械等人才的跨学科团队,并一跃成为湖北省液压领域的领军“新秀”。
广东韶关液压件厂获知后,2006年主动联系液压团队,先研制了1500吨的液压液压试验检测设备,又研发了5000吨和10000吨的检测设备,满足了各种液压设备检测,彻底实现了液压检测设备的国产化。
该厂生产的液压缸有了检测数据后,产品质量值得信赖,产销越来越旺,而全国各地送来检测的业务量也越来越大。厂长高兴地说:“武科大为我们做了一台‘印钞机’。”每年,该老总带队专门来校交流。该企业年产值由几千万提升到2个多亿。
液压团队制定的“液压缸技术条件与试验方法标准”,先批准为广东省地方标准,2015年成为国家标准。之后,为全国十余家企业建立了液压试验检测中心。2013年,该团队再次获得国家技术发明二等奖。
液压团队历经40年发展,由5-6人壮大为如今的60多人,成为湖北省液压界的“领头羊”。83岁的湛从昌教授依然走路精神、思维敏捷,带领着团队老师们致力于解决液压系统的“卡脖子”问题,助力中国工业国产化。